About the project
ARCHITECT: ES
CLIENT & PROJECT MANAGER: Self Builder
PROJECT TYPE: Self build
PRODUCTS: 172mm SIP including internal walls, floors and roof
Fundamental to the broader development of the Stotford Crest Equestrian Centre, the project comprised a three-storey, four bedroomed self-build home. Based within the working grounds of the centre and situated adjacent to the A19 Elwick, Hartlepool, to which the client can relocate with their young family.
The client chose offsite construction to reduce overall build time and minimise disruption to the working livery and stables. In addition, the clients required a premium quality, spacious, thermally efficient home with structural strength to counter the harsh North Sea winds and North East winters whilst having some architectural nuances that made the home truly unique.
Project managed by the client, SIP Build UK were engaged to take complete control and responsibility for the bespoke offsite design, engineer, manufacture, supply and onsite installation of the SIP superstructure including internal walls, floors and additional installation such as steels and masonry support.
A collaborative, underpinned approach enabled the success of the project. With SBUK’s specialised experience in modern methods of construction and assured credentials: STA Gold Assured status, ISO 9001 certified, BBA approved SIP system partnered with the most highly accredited SIP in the UK market, proved very attractive as this guaranteed a mortgage for the project.
The requisites of the build were numerous. Firstly, the site access was via the working ground with livery and stables, and disruption of noise and dust from construction was a key concern. Thus, the need for minimum onsite activity and mitigating disruption was vital. The use of SIPs as the offsite method of construction became ever-increasingly attractive.
Designed offsite, the assured precision engineering, minimal waste and dramatically reduced onsite movement meant reduced CO2 emissions and overall ensured a safer working site. All of which satisfied the client’s requirements.
Secondly, the project needed to achieve the build’s specified thermal and aesthetic requirements whilst remaining within budget. A 150mm soft stone finish, the 172mm SIP panel was selected to achieve a U value of 0.15 without the need for additional insulation, creating a perfect barrier against the cold northerly wind, and many years in a property that uses less energy hence cheaper bills.
Overall construction depth reduced significantly too, compared to more traditional construction methods and reduced onsite labour remarkably. A massive win for a growing family! Thinner walls, more living space! (The saving in wall build-up is estimated to be 176mm all around the build, making a saving of nearly 240 sq ft of additional floor space available).
With an agreed ten week lead time for design, engineering and manufacture, SBUK then delivered the entire SIPs system in just over 3 weeks on site. In addition, SBUK took full control and responsibility for installing the complete frame, including all internal walls, floors and additional structure such as steels and masonry support. One thrilled client!
Boasting 345sq m total floor space, a truly stunning home, integrating well into the local landscape whilst demonstrating sustainable sourcing of the construction materials used.
Self-builders Annie and Phil: “We can’t thank SIP Build UK and our architect, enough and would recommend both without hesitation. Would we do it again and engage SIP Build UK? Yes.”
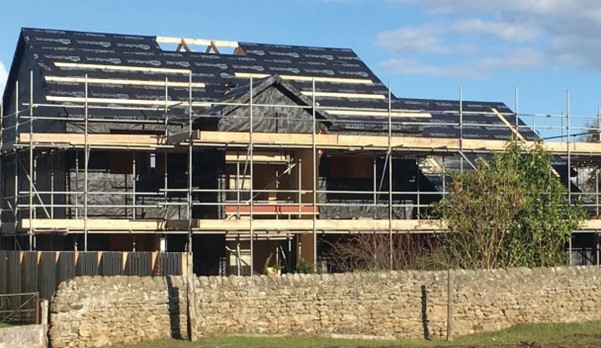
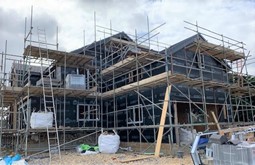
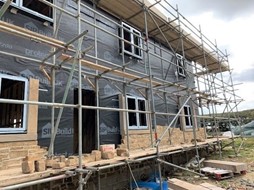
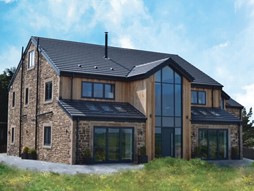
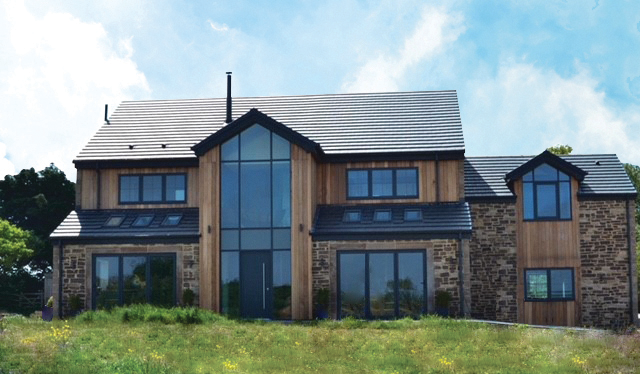

